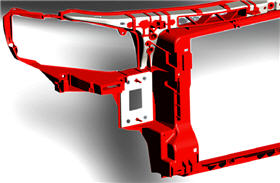 |
Example of a hybrid structure |
Both theoretical studies and components manufactured in series have shown that metal-plastic composites can have better load-bearing properties than open or closed metal profiles. With optimized ribbing, the hybrid components are almost on a par with the closed metal solutions – even under torsional stress – but are more temperature-dependent.
In addition to their cost and weight advantages, hybrid components offer interesting integration and design options, given suitable volumes. By consistently implementing hybrid constructions (with their high precision, integration, and mechanical performance capabilities), component costs can be reduced by up to 30 %, investment costs by up to 50 %, and component weight by up to 40 %.
In the case of structural components that need to respond well to stress (temperature, applied loads and dynamics), different grades of polyamide and different insert materials (steel, aluminum or magnesium as well as continuous fiber-reinforced semi-finished plastics) can be used.
Durethan® (usually PA 6 GF15 – GF60) has proven to be a suitable material for the plastic component.
The design flexibility of the plastic structure allows for optimum component design. This, in turn, facilitates good force distribution in the component and prevents stress peaks. The uniformly distributed product characteristics of Durethan®, which can be reproduced in the finished component, also facilitate challenging designs using CAE.
The production of hybrid components is based on standard injection molding processes using conventional injection molding machines and molds. Use of inserts means that only some additional handling equipment and adjustments to the mold are required.
Hybrid technology is today used in over 70 series applications and 50 million manufactured components.
The 1999 C170 Ford Focus GOR from Ford Motor Company, has been named the 2019 Hall of Fame winner by the Automotive Division of the Society of Plastics Engineers (SPE®).