Hybrid Technology |  | The inspiration for this technology comes from the Greek word “hybrid”, which refers to the different origins and properties of the materials used. |  Hybrid technology unites the properties of two materials, with the combined effect being greater than the sum of the individual parts. It allows geometries that would not be possible with only one material, i.e. large areas using metal or nylon composite sheet or complicated ribbing using injection molding material. Thermoplastics also offer the possibility of functional integration.
Given optimum part design, weight advantages can be realized without compromising on performance (lightweight design), or performance can be improved without increasing weight. Ideally, both can be achieved.
By performing joining processes or other subsequent steps in the injection mold, component production costs can also be reduced.
The injection molding process ensures consistent and reproducible quality.   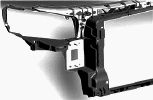 | 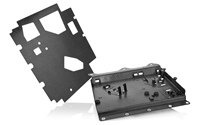 | | | Metal hybrid technology | Hybrid technology with Tepex | The positive (interlocking) fit created between the plastic and the metal inserts of the hybrid component in the injection molding process facilitates the production of extremely strong yet cost-effective components. Compared with conventional injection molding, hybrid technology enables complex structures to be realized that were previously inconceivable using thermoplastics because of their properties. | To increase the application and performance potential of hybrid technology, LANXESS is investigating the use of Tepex® as an alternative to steel sheet and aluminum.
This nylon composite sheet is made of special glass fiber fabrics that are embedded in defined orientations in a thermoplastic matrix – for example, polyamide. | | | If you have any other questions on this subject, please contact us by e-mail. 
The ability to save weight in vehicles by using plastics such as Durethan®, Pocan® and Tepex® leads to increased fuel efficiency and the associated reduction in CO2 emissions. | | | |